The Ultimate Guide to Prefab Building: Revolutionizing Construction
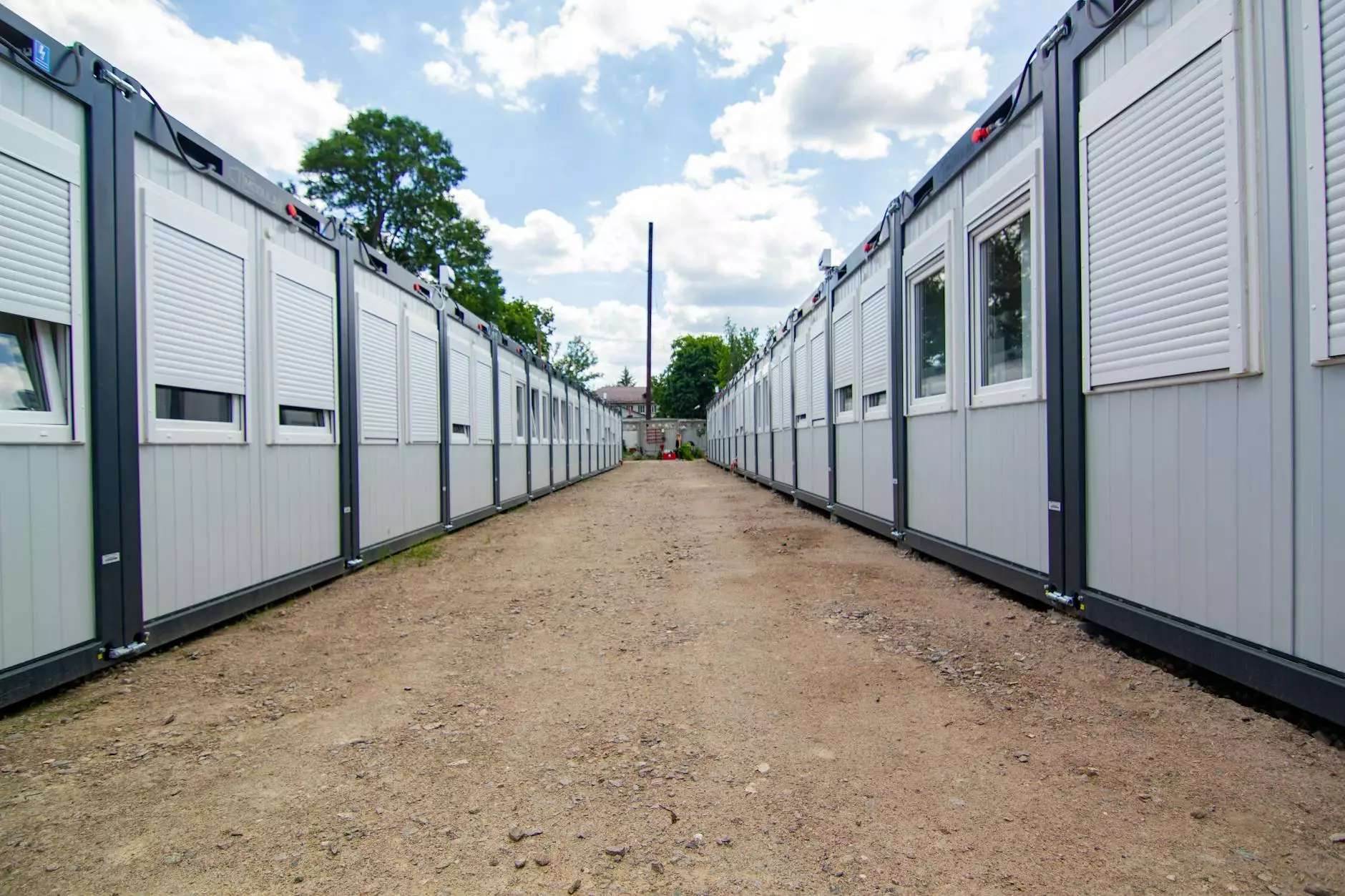
In a world where construction timelines are critical and budgets are tight, the industry has turned to prefab building as a solution that not only accelerates the construction process but also enhances quality and reduces costs. This article delves deep into the world of prefab building, exploring its numerous benefits, the different types of prefab structures, and how to select the right partner for your construction needs.
What is Prefab Building?
Prefab building, short for prefabricated building, refers to structures that are manufactured off-site in advance, usually in standard sections that can be easily shipped and assembled. This method contrasts sharply with traditional construction, where every element is built on-site. Prefab buildings include a variety of structures such as homes, commercial buildings, and modular units tailored for specific applications.
Benefits of Prefab Building
The advantages of prefab building are manifold. Here are some key benefits that make this method increasingly popular among contractors and builders:
1. Time Efficiency
By utilizing prefabricated components, the construction timeline can be significantly reduced. Components are manufactured in a controlled environment while site preparation occurs simultaneously. This parallel processing can shorten the overall project duration by up to 50%.
2. Cost Savings
Prefab buildings can lead to substantial cost reductions. Since construction time is decreased, labor expenses are lowered. Additionally, efficient material usage during manufacturing minimizes waste, translating to budget benefits for both builders and clients.
3. Quality Control
Prefab manufacturers operate in highly controlled environments, which ensures consistent quality across all components. Advanced machinery and techniques reduce human error, resulting in high-quality, durable products that meet strict building codes.
4. Eco-Friendly Solutions
With rising concerns about sustainability, prefab building offers a greener alternative. The efficiency of material usage, reduced waste, and energy-efficient design contribute to a lower carbon footprint compared to traditional construction processes.
5. Flexibility and Customization
Modern prefab buildings offer a variety of designs and customization options that can accommodate different styles and usage requirements. From residential units to commercial spaces, prefabricated structures can be tailored to meet diverse needs.
Types of Prefab Buildings
Understanding the types of prefab building can help in selecting the right solution for your project. Here are the most common types:
1. Modular Buildings
Modular buildings are constructed in sections or modules off-site and then transported to the location for assembly. This method is common in residential homes and commercial spaces, providing high flexibility in design.
2. Panelized Buildings
Panelized systems involve the production of panels that make up the walls, floors, and roofs of a building. These panels are assembled on-site, typically reducing waste and labor costs.
3. Pre-cut Buildings
Pre-cut buildings consist of materials that are measured, cut, and labeled at the factory before being sent to the construction site. This approach allows for quick assembly and is often ideal for DIY projects.
4. Complete Prefab Solutions
Many companies offer complete prefab solutions, including plumbing, electrical, and HVAC systems all integrated into a single structure. This option provides a convenient all-in-one solution for builders and contractors.
How to Choose the Right Prefab Building Manufacturer
Choosing a reputable prefab manufacturer is crucial to the success of your project. Here are some tips to keep in mind:
1. Research Experience and Reputation
Look for manufacturers with a proven track record of delivering quality prefab buildings. Read reviews, check their portfolios, and ask for references to assess their reliability.
2. Inspect Quality and Standards
Ensure that the manufacturer adheres to strict quality control processes and complies with local building codes and regulations. This is vital for the safety and durability of your structure.
3. Evaluate Customization Options
Choose a manufacturer that offers flexibility in design and customization. The ability to tailor a prefab building to your specific needs minimizes compromise and maximizes satisfaction.
4. Compare Costs and Services
Request detailed quotes from several manufacturers and compare not just the costs, but also the scope of services offered. Consider warranties and post-construction support as part of the overall value.
Understanding the Process of Prefab Building
The prefab building process can be broken down into several stages, each important to ensure a successful outcome:
1. Design and Planning
The first step in any prefab building project is thorough design and planning. This stage often involves collaboration between architects and clients to establish the desired specifications, layout, and customization options.
2. Manufacturing
Once plans are finalized, components are manufactured in a factory setting. This includes cutting, assembling, and finishing each section of the building with precision.
3. Transportation
After completion, the modules or components are transported to the construction site. Proper logistics management is essential to ensure timely and safe delivery.
4. Assembly
Upon arrival, the pieces are assembled according to the project plan. This phase typically involves setting the modules in place using cranes and ensuring that all connections are secured.
5. Finishing Touches
The final step includes adding the finishing touches such as painting, landscaping, and installing utilities, turning the prefab structure into a functional space.
Case Studies: Successful Prefab Building Projects
Numerous real-world examples highlight the effectiveness and efficiency of prefab building. Here are a few notable projects:
1. The Koda by Kodasema
This compact, modular home is designed for fast assembly and minimal environmental impact. Installed in just a few days, it exemplifies how prefab buildings can combine aesthetics with practicality.
2. The Living Homes
A pioneer in modern home building, Living Homes delivers sustainable residences that are prefabricated for energy efficiency. Their projects have set new standards in design and sustainability.
3. Factory-built Schools
Across the globe, many schools have been rapidly constructed using prefab techniques, addressing urgent needs in education while maintaining quality and safety protocols.
Future Trends in Prefab Building
The future of prefab building looks promising, with several trends shaping its evolution:
1. Smart Technology Integration
Smart homes and buildings are becoming the norm. Future prefab constructions will likely include integrated technology for energy management, security, and convenience.
2. Sustainable Materials
With a global push towards sustainable living, the use of eco-friendly materials in prefab construction is on the rise, helping to lower environmental impact further.
3. Increased Customization
As consumer preferences evolve, the demand for personalized living spaces will grow, pushing manufacturers to offer more customization options.
Conclusion
The prefab building industry is revolutionizing construction, providing innovative solutions that cater to modern needs. With benefits like time efficiency, cost-effectiveness, and design flexibility, it's no surprise that this building method is fast becoming a preferred choice for contractors and clients alike. Whether you're looking to build a home, an office, or a larger commercial structure, considering a prefab building solution could be the key to achieving your construction goals successfully.
Call to Action
If you're interested in exploring prefab building options for your next project, visit Module T today. Discover how our expertise in building supplies and contractor services can help bring your vision to life!