The Importance of Plastic Injection Tools in Metal Fabrication
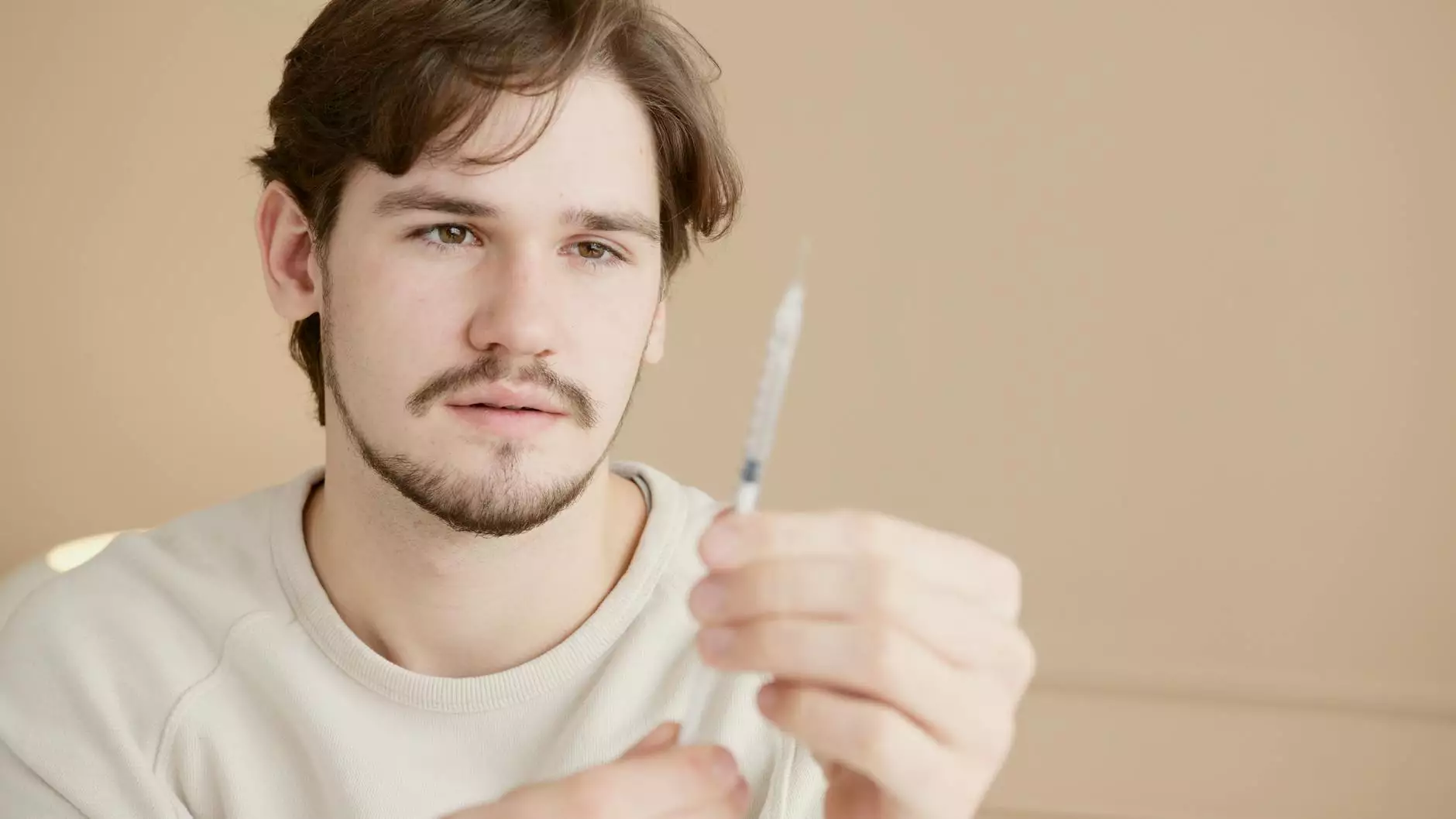
In today’s manufacturing landscape, plastic injection tools have emerged as a fundamental component, particularly within the field of metal fabrication. These tools not only streamline the production process but also enhance the overall efficiency and quality of products. This article delves into the essentials of plastic injection tools, their benefits, applications, and their immense significance for businesses, particularly those in the metal fabrication sector.
Understanding Plastic Injection Molding
Plastic injection molding is a process that involves creating plastic parts by injecting molten material into a mold. This method enables the mass production of items that are consistent in quality and precise in dimensions. The success of this process largely depends on the quality and design of the plastic injection tools used.
How Plastic Injection Tools Work
The basic mechanism of plastic injection tools involves several key phases:
- Melting: Plastic pellets are heated until they melt, transforming into a viscous liquid.
- Injection: The melted plastic is then injected into a pre-defined mold under high pressure.
- Cooling: The injected plastic cools and solidifies, taking the shape of the mold.
- Ejection: Once the part has cooled, it is ejected from the mold and prepared for secondary operations if needed.
The Benefits of Using Plastic Injection Tools
Businesses engaged in metal fabrication can gain a myriad of advantages by incorporating plastic injection tools into their operations. Here are some of the primary benefits:
1. Increased Production Efficiency
Plastic injection tools are designed for high-volume production. Their ability to produce highly consistent and accurate parts means that manufacturers can achieve greater throughput, thereby increasing overall efficiency.
2. Cost-Effectiveness
While the initial investment in plastic injection tools can be substantial, the long-term savings are significant. The durability and longevity of these tools mean less frequent replacements and lower production costs over time.
3. Versatility in Design
Modern plastic injection tools are incredibly versatile, allowing for intricate and complex designs that might be challenging to achieve with other manufacturing methods. This versatility includes:
- Production of parts with various shapes and sizes
- Ability to incorporate multiple materials or colors in a single run
- Facilitating the production of lightweight but sturdy items
Applications of Plastic Injection Tools in Metal Fabrication
The use of plastic injection tools is not limited to one industry; they find applications across various sectors within metal fabrication:
1. Automotive Manufacturing
In the automotive industry, plastic injection molded parts are extensively used for components like dashboards, bumpers, and housings for electronic components. The ability to produce lightweight parts helps in enhancing fuel efficiency.
2. Consumer Electronics
From mobile phone cases to remote control housings, plastic injection tools are used to create parts in consumer electronics that are not only functional but also aesthetically pleasing.
3. Industrial Equipment
Machinery and tools often utilize components made from plastic injection molding, which can reduce weight without sacrificing strength, leading to more efficient machinery operations.
4. Medical Devices
The medical field benefits significantly from precise, reliable, and sterile plastic components created through injection molding. This includes items such as syringes, surgical tools, and housing for various devices.
Improving Quality with Advanced Plastic Injection Tools
Quality assurance is critical in any manufacturing process. Advanced plastic injection tools implement state-of-the-art technology to ensure precision and consistency. Some of the innovations redefining the landscape include:
1. Enhanced Mold Design
Today, mold designs are optimized using computer-aided design (CAD) software which allows for simulations and adjustments before actual production starts. This leads to better efficiency and reduced waste during the manufacturing process.
2. Smart Monitoring Systems
Implementing smart sensors within plastic injection tools allows manufacturers to monitor the entire production process. Data collected can lead to improved processes, minimized downtime, and enhanced quality control.
3. Sustainable Practices
Modern plastic injection tools also focus on sustainability. Manufacturers are utilizing recyclable materials, minimizing waste, and optimizing energy usage, thus aligning with green manufacturing practices.
Choosing the Right Plastic Injection Tools
When selecting plastic injection tools, several factors need consideration:
- Material Compatibility: Ensure the tools are appropriate for the specific type of plastic used.
- Mold Quality: Invest in high-quality molds that can withstand the pressure and heat of the injection process.
- Manufacturer Reputation: Work with reputable suppliers who offer reliable products and support.
- After-Sale Service: Assess if the supplier provides maintenance and repair services for the tools.
Conclusion
In conclusion, plastic injection tools are invaluable to the metal fabrication industry, enhancing production efficiency, reducing costs, and providing versatility in product design. As technology evolves, these tools will continue to play a pivotal role in a range of industries, pushing the boundaries of what is possible in manufacturing. By selecting the right plastic injection tools, businesses can significantly improve their operational capabilities, achieve higher quality outputs, and remain competitive in an ever-evolving marketplace.